Technology
The concept of finishing metal surface by applying dry powders, which after fusion form continuous and integrated coatings was developed in 1950’s. Initially thermoplastic resins were used but then thermosetting powders were developed which open up much wider field of use.
Here we can classify the powder coatings according to its main chemistry i.e.
- Thermoplastic Powder coatings: In these cases powder coatings can be reshaped after their first application as the changes in the properties are not permanent
- Thermosetting Powder coatings: With these powders we can not reshape it after first application as the chemical changes taking place are permanent. Thus it is not a reversible reaction
The increasing use of thermosetting powders has been necessary because of the need to reduce air and water pollution coupled with the fact that with today’s rising costs of basic raw materials and labors, powder coatings is often a variable commercial consideration when compared to conventional industrial liquid coatings/paints.
Powder coatings verses Liquid coatings-
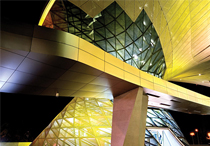
Some of more obvious advantages of using thermosetting powders are:
a) It is ready for use: They are immediately ready for use. They do not have to be mixed with any other ingredients such as solvents, catalyst etc. This saves on shop floor time and also eliminates a variable which it is vital to control with liquid paints to obtain satisfactory film properties.
b) Reduction in fire risks: No solvent involved in the powder coatings greatly eliminates the fire risks which also gives cost saving on statutory safety features in plant, reduce insurance premium and saving can be made on manpower time.
c) No costly wastage of solvents: Environmental cleanliness.
d) No effluent disposal problem: With liquid paints system, water wash spray booths are commonly employed. The overspray is usually emulsified in the water, which in some cases is put directly to drain or in other cases allowed to settle out in sludge tanks. Powders do not give rise to these problems and extra costs.
e) No air pollution: Over sprayed powder is recoverable and no powders need escape into the atmosphere.
f) Reduction in health hazard to operators: There is reduction in health hazards to the operators as powders do not contain solvent. There is remarkable reduction in nose, mouth and throat irritation as is sometimes noticeable particularly during hot weather in liquid paint shop.
g) Concern in recent years about possible mutagenic effects of TGIC-one of the materials commonly used in powder coatings, has been replaced after development of TGIC free products provides an alternative option.
h) Considerable improvements have also been made in reducing the heavy metal content of powder; in particular Lead. Lead free products are now achievable for the vast majority of the shades.
i) 95 % powder utilization: With powder coatings it is possible to maintain material loss below 5 % by controlling the overspray and over sprayed powder can be mixed with virgin powder to achieve 95 % powder utilization.
j) Controlled film thickness: It is easier than the liquid coatings. More controlled, uniform and even thicker coating is possible by one coat application only.
k) Variety of coatings: It is possible to achieve different gloss levels; ranges from 0-100 % {dead matt – Super glossy}, smooth to textured etc. Also choice of the polymer type can optimize properties such as chemical resistance and exterior durability.
Classification based on the gloss level.
1. Super glossy – Above 90%
2. Gloss - More than 75-90%
3. Semi glossy - 50 to 75%
4. Satin/silk - 20 to 50%
5. Matt 10-20%
6. Super matt – 5-10%
7. Dead matt – Less than 5%
Classification based on the polymer used:
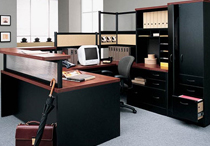
Epoxy Powder Coatings: - Here epoxy resins are main polymer which is cured by suitable cross linker. This kind of powder will give super glossy to dead matt appearance also smooth to textured finish. These powders are used where strong chemical resistance to the coating is required, along with good mechanical properties like, adhesion and flexibility. But there is a major drawback of these powder coatings it tends to yellow on over beak more rapidly compared to other systems. Also its exterior durability is poor due to presence of peroxides ring which on out door exposure feds & chalks rapidly. Hence these powders are recommended only for interior application. Film curing is an addition mechanism hence no elimination of volatiles during curing.
Typical Uses:
- Laboratory fittings and fixtures can be provided after testing.
- Machine Tools
- Color Availability:
- Customized - Corporate Colours
- Pantone
- RAL Ranges
- IS
- Powder Coating Finishes Include:
- Texture
- Leatherette/River (Structure)
- Smooth
- Availability:
- Low cure formulations
- Anti-gassing formulations
- Tribo/Corona applicable formulations
- Gloss Levels:
Powder Coatings are available in a variety of gloss levels from Dead Matt (1%) to Full Gloss (over 90%). - Please contact us as we can match to your specific requirements.
POLYESTER POWDER COATINGS
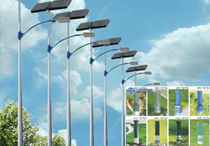
A series of finest grade polyester powders, which exhibit excellent weathering characteristics on exterior surfaces. The film is tough and flexible, resists cracking and flaking when applied over the proper pretreatment.
Also low cure anti-gassing edition can be supplied in polyester coatings. Polyester powders are also available in TGIC free
.
Typical Uses:
- Automobile and Cycle Components
- Garden Furniture
- Lighting Fixtures and Fittings
- Special requirements for Outdoor Use Electrical Equipment can be provided.
- Color Availability:
- Customized - Corporate Colors
- Pantone
- RAL Ranges
- IS
- Powder Coating Finishes Include:
- Texture
- Hammer
- Leatherette/River (Structure)
- Wrinkle
- Availability:
All powder coatings are available in:- - Low cure formulations
- Anti-gassing formulations
- Corona/Tribo applicable formulations
- TGIC Free formulations
- Gloss Levels:
Powder Coatings are available in a variety of gloss levels from Matt (2%) to Full Gloss (over 85%). -
Along with standard Polyester Powder Coatings, TALISMAN THERMOCURE POWDER COATINGS can offer Super Durable Polyesters. These have increased exterior durability properties, making them ideal when protection is needed in the harshest outdoor environments.
Please contact us as we can match your requirements.
EPOXY-POLYESTER POWDER COATINGS
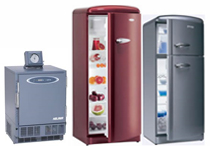
A blend of epoxy and polyester resins, which offer both designer and coater the most advantageous combination of decorative and protective properties on a wide range of internal components. It combines speed of use, well over bake stability with excellent colour and gloss retention.
Depending on the choice of the resins their relative properties varies between those of epoxy and polyesters. The presences of epoxy resin still leave the coating susceptible to exterior exposure.
These products are for use where good chemical and detergent resistance is required, combined with excellent decorative appearance and ease of application it offers well over bake stability.
Also available low cure and low cure anti-gassing finishes.
Typical Uses:
- Special requirements for electrical enclosures can be provided.
- White goods
- Light fittings
- Office furniture
- Business machines
- Color Availability:
- Customized - Corporate Colors
- Pantone
- RAL Ranges
- IS
- Powder Coating Finishes Include:
- Texture
- Antique
- Smooth
- Leatherette/River
- Metallic
- Availability:
All powder coatings are available in:- - Low cure formulations
- Anti-gassing formulations
- Tribo applicable formulations
- Corona applicable formulations
- Gloss Levels:
Powder Coatings are available in a variety of gloss levels from Matt (5%) to Full Gloss (over 85%).Please contact us as we can match to your specific requirements.
POLYURETHANE POWDER COATINGS
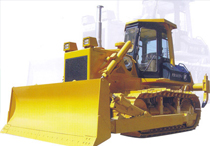
hese are based on hydroxyl terminated polyester reacted with blacked/internally blocked, isocynates. They provide good all round chemical resistance and good exterior durability where a high degree of performance and appearance is important. This product exhibits good heat resistant properties, as well as good flow and weather resistance. These coatings provide exceptional smoothness.
Typical Uses:
- Interior Use
- Exterior Use
- Domestic Appliances
- Electrical Switchboxes
- Bus Shelters
- Radiators & Heaters
- Ventilation Equipment
- Automobile & Cycle Components
- Color Availability:
Customized - Corporate Colors
Pantone
RAL Ranges
IS
Powder Coating Finishes Include:
Texture
Smooth
Leatherette/River
Availability
All powder coatings are available in:-
Anti-gassing formulations
Corona applicable formulations - Gloss Levels:
Powder Coatings are available in a variety of gloss levels from Matt (5%) to Full Gloss (over 85%). Other special powders like low bake, rapid cure, low film thickness(35-45 microns),Wrinkle finish, Heat resistance powders, Electrical insulation coatings; TGIC free formulations with H.A.A. & Glycidyl esters(PT 910), Antigraffitee coatings etc can be provided. - Please contact us as we can match to your specific requirements.
MANUFACTURING
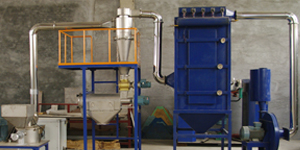
Manufacturing process of the powder coatings includes following processes-
- Mixing of the various raw materials.
- Hot melt compounding of the premix which is called as extrusion.
- Settling and cooling of hot material
- Fine grinding – finish product.
During the process we do very striengent quality parameter checks to insure the product quality.
- Dry film thickness: A simple instrument called DFT meter is used to measure the coating thickness on the substrate. These methods are based upon high frequency eddy current and electromagnetic induction.
- Gloss: It is relative luminous reflectance factor of a specimen in mirror direction. It represents the ratio of luminous flux reflected from a specimen to the luminous flux reflected from the standard surface under similar geometric conditions. According to standards the standard surface is polished glass.
The measurement can be done with 20°, 45°, 60°and 85° angle.
Mechanical properties:
Hardness of the cured film: There are various methods described in corresponding standards for measurement of hardness of the coating like indentation hardness, pendulum hardness, and pencil hardness. The most simple and commonly used popular method is pencil hardness test by using square shaped graphite pencils. It is measure don the hardness scale from 6B to 6H. The hardness is reported as a grade of the hardest pencil that does not cause any marring of the surface.
Flexibility test: With this method one can conclude the resistance to elongation of the coating. Mandrel bend tests consist of bending the coated material panel over metal support of cylindrical or conical shape. In case of cylindrical mandrel the test results are reported as the smallest diameter of bending at which a crack of the coated surface is not detected by unaided eye. When conical mandrel is used as a support the test results are reported as the distance from the small end of the cone to the end of the crack in the panel.
Impact: With this test we can measure the strength of the coating to the rapid deformation. A known weight from known height is allowed to fall on the coating surface and the results are reported as the maximum kg.cms or pound. Inch value obtained at which there is no cracking of the film.
Adhesion: The so-called cross-cut adhesion test is the common test method for assessment of the adhesion of the powder coating to the substrate. A series of parallel cut are made with a special knife in the film deep enough to touch the metal surface. A second series of parallel cuts are made at right angles to the first. By means of pressure sensitive adhesive tape the square which are lost from the surface are pulled of and are measured as GT-0/100 or 5B to 0B depending on the percentage of the affected area of the lattice.